Lately I still look around the internet and search for which connectors I should use for my 6s (25,2 Volt), 10s(42,0 Volt) or 14s(58,8 Volt) battery setup, and which connectors I should use from the speed controller to connect the brushless engine. The voltage is a factor for choosing a connector but the most important factor is the amount of AMP’s is should handle.
When using connectors undersized in your pressures model can result in melting connector which can de-solder.
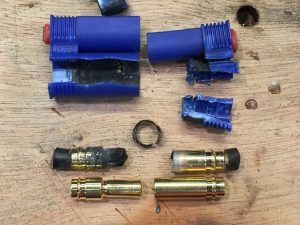
The connector should never be the bottle neck in the system. For example the logo 400 SE has a 70Amp speed controller which is capable to feed continuously 70Amp to the engine. The connector from battery to the speed controller should be capable to guide the 70 amps but also the three connectors to the engine.
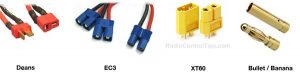
As a reference and look-up table I always refer to a German website: Elektromodellflug.de. This page gives a good overview off all standard connectors on the market. There are 2 pages, Page_1 and Page_2.
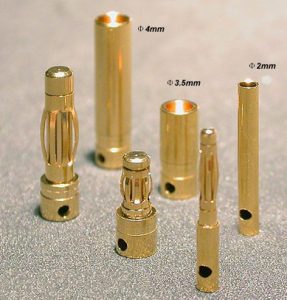
Most common Lipo battery connectors are the XT series (30-60 or 90). If there are connectors solded on your new battery pack the biggest change that these connected. These are very good connectors and even available with an anti-spark system. The rating 30-60-90 represents the maximum current the connector can withstand.
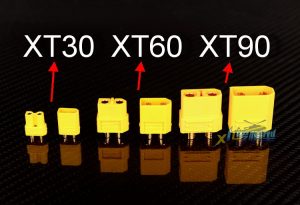
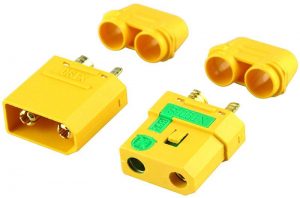
So what do I use? For the logo 400 SE with 6s batteries (3000mAh * 40C = 120Amps) I use EC5 (5mm connectors) and 5mm standard gold connectors between the speed controller and the engine. These 5mm connectors handle 80 Amps continuously. Perfect because the hacker x70 pro speed contoller uses 70Amps max in my flight style. Furthermore I used EC connectors instead of XT connectors because all of my friend already switched to EC and when flying on a field is is handy to exchange batteries and charge each other batteries. Otherwise I would have used the XT instead!
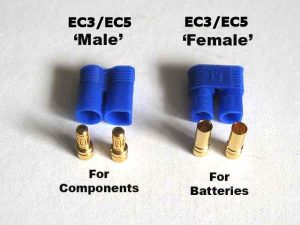
The Rigid2 which uses 14s Lipo’s (65C) capable of delivering 4.400mAh*65C = 292,5 Amps and a speed controller Kosmik 200HV which can handle 200Amps continuously and 400Amps peak need different connectors. Knowing the engine can handle 6,5 kWatt continuously which represents 6500Watt/58,8Volt=110Amps! This all needs “special” connectors and special methods in order to prevent the connectors from overheating which could result in de-solder the connetors during load. The connectors between the batteries and speed controllers are AS150 connectors with anti spark (7mm connectors which can handle 150 amps continuously). But I don’t want 7 to 8mm connectors between the speed controller and engine, I solder the cables together. No connector, no heat dissipation so best connection there!
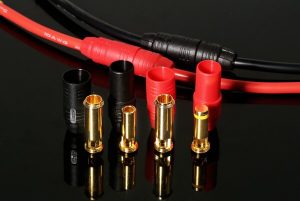
I prefer the EC5 connectors and 5mm connectors for normall use… and when batteries are larger then 6s I use anti spark connectors when the speed controller has no anti spark system in the controller. Currents above 100Amps theoretically use the AS15o connectors for the batteries and at least 6mm or bigger to the engine.
Last but not least, don’t forget to use wires in a diameter suitable for the right current, for batteries and speed control in the engine.
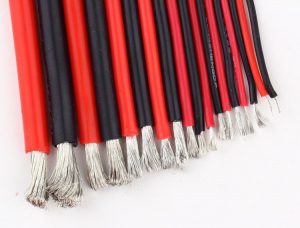
Hope this information helps 😉